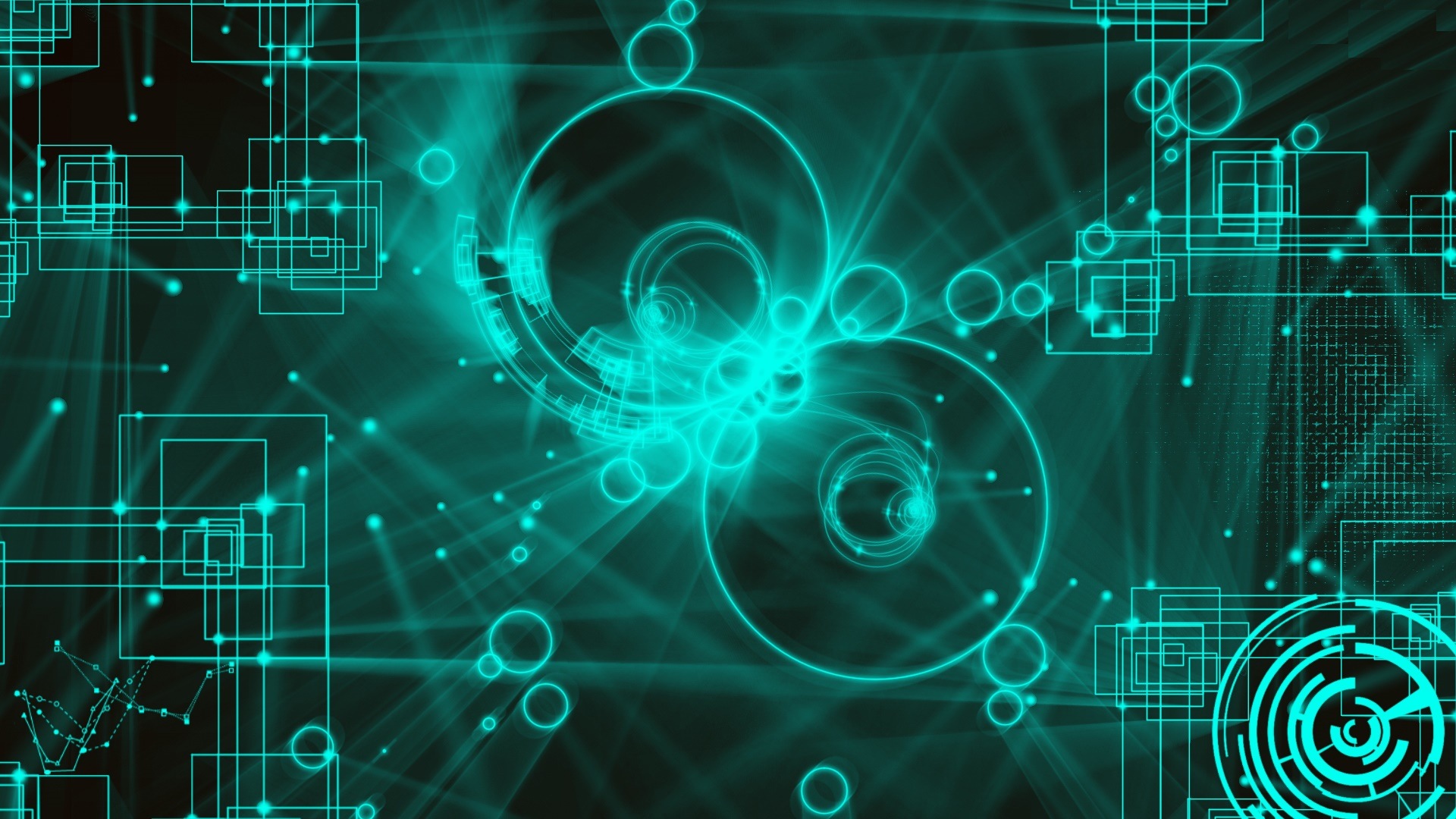
SystSoftPcCelTv
Membros-
Posts Por Dia
0.19 -
Posts
537 -
Registrado em
-
Última visita
-
Créditos EBR
1,641 [ Doar ]
Tipo de Conteúdo
Fórum
Downloads
Blogs
Galeria
Assinaturas
Calendário
Tudo que SystSoftPcCelTv publicou
-
certissimo
-
-
Olá Pessoal! Nesse projetinho de pisca led na protoboard não funciona. Fiz no proteus e o mesmo funciona normal, no entanto na protoboard ele não roda. Compilei no mplab carreguei no proteus e funcionou. Fiz no ccs c carreguei no proteus e funcionou. No entanto na protoboar não roda. 5V de alimentação. //Carrega a biblioteca para o microcontrolador PIC16F722a #include <16F722A.h> //Configuracao FUSES #FUSES NOWDT #FUSES INTRC_IO #FUSES NOPUT #FUSES NOPROTECT #FUSES NOBROWNOUT #FUSES NOMCLR //Define a utilização do clock interno de 16 Mhz #use delay(clock=16000000) #define PINOLED PIN_B1 //Pino ao qual o led esta ligado void main() { while (1) { output_bit(PINOLED, TRUE); // Liga o Led delay_ms(500); // Aguarda 1/2 segundos output_bit(PINOLED, FALSE); // Desliga o Led delay_ms(200); // Aguarda 1/2 segundos } }
-
 resolvido STI-1422/R42ii1-37gr42000-10/Não da video, sem vcore.
SystSoftPcCelTv respondeu o tópico de Manoel74 em Casos resolvidos - Notebooks
@Manoel74 olá! você tem alimentação e habilitação no pu9? -
 dúvida Gigabyte - GA-G31M-S2L - liga e nao da imagem
SystSoftPcCelTv respondeu o tópico de João Victor de Oliveira em Motherboards, PCs, All in One & Cia
Ela não está dando vídeo na on-board ou na placa de vídeo? Por outro lado você precisa de uma placa de diagnóstico básica que faz simplesmente analisar os códigos de erro oferecidos pela Bios do computador durante seu período de POST caso o bios estivesse ok, Esse aquecimento chega a quantos graus cesius lá no vcore? -
 notícia Samsung Electronics desenvolve a primeira tecnologia de empacotamento de chips 3D-TSV de 12 camadas do setor
SystSoftPcCelTv postou um tópico em Notícias
Samsung Electronics desenvolve a primeira tecnologia de empacotamento de chips 3D-TSV de 12 camadas do setor. A nova tecnologia permite o empilhamento de 12 chips DRAM usando mais de 60.000 furos TSV, mantendo a mesma espessura que os atuais chips de 8 camadas A Samsung Electronics, líder mundial em tecnologia avançada de semicondutores, anunciou hoje que desenvolveu a primeira tecnologia 3D-TSV de 12 camadas (Through Silicon Via) do setor. A nova inovação da Samsung é considerada uma das tecnologias de embalagem mais desafiadoras para a produção em massa de chips de alto desempenho, pois requer precisão para interconectar verticalmente 12 chips DRAM através de uma configuração tridimensional de mais de 60.000 furos TSV, cada um dos quais é um -extrai a espessura de uma única mecha de cabelo humano. A espessura do pacote (720㎛) permanece a mesma dos produtos atuais de alta largura de banda de memória de banda dupla 2 (HBM2), o que representa um avanço substancial no design de componentes. Isso ajudará os clientes a lançar produtos de alta capacidade e de próxima geração com maior capacidade de desempenho sem precisar alterar os designs de configuração do sistema. Além disso, a tecnologia de empacotamento 3D também apresenta um menor tempo de transmissão de dados entre os chips do que a tecnologia de ligação de fio atualmente existente, resultando em velocidade significativamente mais rápida e menor consumo de energia. "A tecnologia de embalagem que protege todos os meandros da memória de desempenho ultra-poderoso está se tornando tremendamente importante, com a ampla variedade de aplicativos da nova era, como inteligência artificial (IA) e computação de alta potência (HPC)", disse Hong-Joo Baek , vice-presidente executivo do TSP (pacote de teste e sistema) da Samsung Electronics. “À medida que a expansão da lei de Moore atinge seu limite, espera-se que o papel da tecnologia 3D-TSV se torne ainda mais crítico. Queremos estar na vanguarda dessa tecnologia de embalagem de chips de última geração. ” Baseando-se em sua tecnologia 3D-TSV de 12 camadas, a Samsung oferecerá o mais alto desempenho de DRAM para aplicativos com uso intensivo de dados e velocidade extremamente alta. Além disso, ao aumentar o número de camadas empilhadas de oito para 12, a Samsung em breve poderá produzir em massa 24 Gigabytes (GB) * de alta largura de banda de memória, o que fornece três vezes a capacidade de 8 GB de alta largura de banda no mercado hoje. A Samsung poderá atender à crescente demanda do mercado por soluções HBM de alta capacidade com sua tecnologia de ponta TSV 3D de 12 camadas e espera solidificar sua liderança no mercado de semicondutores premium. * Produto de produção em massa de 8 GB = 8 GB x 8 camadas, produto desenvolvido em 24 GB = 16 GB x 12 camadas * Estrutura de seção transversal PKG * Ligação de arame vs tecnologia TSV fonte -
 em análise HP PAVILION 14- Placa- DAY11AMB6E0 REV:E- Não liga
SystSoftPcCelTv respondeu o tópico de Tiago Wanderley em Notebook's
@Tiago Wanderley olá! E o p10 está ok? E o curto é total? -
 em análise ECS - TIGD-CI4 - não reconhece sata
SystSoftPcCelTv respondeu o tópico de barbosa barreto em Motherboards, PCs, All in One & Cia
O esquema que estou consultando é o TIGD-CI3 torcendo pra não ter tanta diferença. O pch também atua no controle da porta sata. Mas antes que eu me esqueça, e eu imagino que você já fez a parte básica de todo o conserto que é ver setup, ver o cabo de dados e da alimentação da porta sata, testar outras mídias - ver se tem oxidação- ter feito uma boa limpeza, tanto do conector quanto da placa e etc. Por outro lado pode ser um simples capacitor na linha de dados, mas suponho que todas as portas esteja ruins. Aí aponta para um problema no controlador. Comece com um pouco de fluxo e M.E (moderado aquecimento sobre ele) Lembrar também que e.m.i - interfere muito em transmissão de dados. -
 em análise ECS - TIGD-CI4 - não reconhece sata
SystSoftPcCelTv respondeu o tópico de barbosa barreto em Motherboards, PCs, All in One & Cia
@barbosa barreto olá !Todo processo de aquecimento de placa e componentes nela presente requer o controle da temperatura e do processo em si. Os processos feitos por maquinas seguem uma curva de aquecimento em que você sabe exatamente quando a solda começa a derreter. Essa temperatura ela é atingida por um aquecimento dividido: Você aquece a base da placa e vai também calor sobre o componente especifico que se quer trabalhar. E essas duas fontes de calor desenham uma curva que te permite maior segurança para trabalhar. O que não quer dizer que o quê se faz com a maquina não seja possível ser feito sem ela. A unica diferença é que o controle "pid" (controle de variáveis) fica por conta do técnico e não da maquina. Se o calor vier só de uma fonte; por exemplo, estação de ar quente por cima do componente - dependendo do componente pode queimar ou criar bolhas. Para evitar isso eu entende que traz muito mais segurança ter uma fonte de calor por baixo da placa, levando ela gradativamente até 150 -180°c . Antigamente quando as soldas não tinha prata, 180º C já derretia a solda. Hoje com as placas mais modernas lead free(sem chumbo) derretem somente com 217°C por isso o cuidado com os componentes que não suportam essa temperatura tem que ser verificado - capacitor eletrolítico, por exemplo, pode estourar. Por isso tem que haver uma proteção com fita kapton, com papel alumínio - deixando exposto somente a área onde vai o calor. No caso desse componente que você pretende trabalhar, você pode colar sobre ele um pedaço de fita de alumínio adesiva que é mais barata que a kapton e é tão eficiente quanto e aplicar calor de forma gradativa circularmente em volta dele. Observando que o calor que se aplica por cima ele é complementar à temperatura que você já tem na base - então se eu tenho 170/180° C na base, eu vou a partir daí gradativamente chegando até a temperatura necessária para remove-lo ou solda-lo. Então nessa subida de tempos em tempos você dá um leve toque lateral para saber se ele já descolou. O ponto de fusão da solda lead free é 217°C e as vezes se chega ao 220°c por uma má distribuição do calor principalmente por baixo do chip. Também é bom observarmos quais componentes estão envolta desta área onde vai o calor e protege-los um pouco mais, ou remove-lo quando possível. Peças plasticas, por exemplo, quanto mais proteção melhor. Pra te ajudar você tem que ter um termômetro infravermelho, que não tão caro. tá joia! -
 em análise ECS - TIGD-CI4 - não reconhece sata
SystSoftPcCelTv respondeu o tópico de barbosa barreto em Motherboards, PCs, All in One & Cia
-
 dúvida tv philco PH32E20DSG flash corrompida
SystSoftPcCelTv respondeu o tópico de Bruno Miguel Dias Sancho em TVs de PLASMA, LCD, LED e CRT
@Bruno Miguel Dias Sancho olá ! eu tenho este arquivo PH32E20DSGWAVA.img serve?- procedimento via usb. Não sei se está bom. -
 em análise Fonte Vinik 600w / Não Liga
SystSoftPcCelTv respondeu o tópico de XKing Infinityx em Fontes & No-Breakes
@XKing Infinityx ! quanto de tensão tem nos capacitores principais no primário. Verifique também se tem curto na saídas de 12v. 3.3v , 5v etc. -
 em análise ECS - TIGD-CI4 - não reconhece sata
SystSoftPcCelTv respondeu o tópico de barbosa barreto em Motherboards, PCs, All in One & Cia
@barbosa barreto olá! Verifique se tem o integrado IT8721F-DX em sua placa. Tendo verifique a tensão no pino 99 do mesmo. -
 em análise Positivo C1260 - 71R-H14BT4-T830 REV. 3.0 - Não dá imagem na tela integrada
SystSoftPcCelTv respondeu o tópico de XkawagataX em Notebook's
olá ! O painel precisa estar energizado para ser detectado e somente apos isto teríamos as habilitações dos integrados para o seu controle. Para tanto precisa só do +3.3V_LCD , ou talvez do VIN_LCD também; não tenho certeza. No entanto ambos são comandados pelos sinais PANEL_3.3V_ON e LVDS_VIN do super i/o. Como você tem 0v no gate dos transistores que liberam essas tensões, das duas uma: Ou o super i/o está com problema ou você está perdendo esses sinais sobre algum componente por aterramento por defeito. Pelo seu relato se isto estiver acontecendo é mais provável que seja em cima do circuito de +3.3v_LCD. Então testes estes três componentes r175,c190 e q43 : -
 em análise Tv Sony, KLD 22EX425, Listras coloridas na metade da tela.
SystSoftPcCelTv respondeu o tópico de julioduarte em TVs de PLASMA, LCD, LED e CRT
veja o sinal lvds se está ok. Faça um M.E com fluxo - no chip que é o suspeito de estar com problema . -
 em análise Positivo C1260 - 71R-H14BT4-T830 REV. 3.0 - Não dá imagem na tela integrada
SystSoftPcCelTv respondeu o tópico de XkawagataX em Notebook's
-
 em análise Positivo C1260 - 71R-H14BT4-T830 REV. 3.0 - Não dá imagem na tela integrada
SystSoftPcCelTv respondeu o tópico de XkawagataX em Notebook's
Eu tava com mais de um esquema aberto - devo ter me confundido. o que estou olhando é este Shuttle 71R-H14BT4-T830 - H14BT01-4L. -
 em análise Positivo C1260 - 71R-H14BT4-T830 REV. 3.0 - Não dá imagem na tela integrada
SystSoftPcCelTv respondeu o tópico de XkawagataX em Notebook's
@XkawagataX é o sinal BLON. Pra vermos se ele tá ligado. -
 em análise Positivo C1260 - 71R-H14BT4-T830 REV. 3.0 - Não dá imagem na tela integrada
SystSoftPcCelTv respondeu o tópico de XkawagataX em Notebook's
@XkawagataX olá! você tem tensão no dreno do q31? -
 devolvido Dell Inspiron 5470 / Quanta DAJW8CMB8E1 / não liga
SystSoftPcCelTv respondeu o tópico de Sergio Penido em Notebook's
-
 dúvida Azamerica S2005 3D - identificação do UP05
SystSoftPcCelTv respondeu o tópico de quitomoreno em Identificação e Equivalência de Componentes
@quitomoreno Olá! se não houver alguém no fórum com a referencia dele, você terá que investigar como é a pinagem na placa. De onde vem os 12v , onde é o gnd é onde é a saída de 5v volts. Se tem feedback. Por exemplo, este c.i entrega 5v a partir de 12v, porem tem a questão da pinagem.: https://br.mouser.com/Semiconductors/Power-Management-ICs/Voltage-Regulators-Voltage-Controllers/LDO-Voltage-Regulators/Datasheets/_/N-5cgac?P=1yx5k7vZ1z0shyuZ1z0wa29Z1z0z7v7Z1z0z7pt -
 devolvido Dell Inspiron 5470 / Quanta DAJW8CMB8E1 / não liga
SystSoftPcCelTv respondeu o tópico de Sergio Penido em Notebook's
@Sergio Penido olá! Veja se o SIO recebe o sinal eDP_BL_EN (pino 120) e se sai dele o sinal LCD_BAK no pino 35. -
 dúvida Azamerica S2005 3D - identificação do UP05
SystSoftPcCelTv respondeu o tópico de quitomoreno em Identificação e Equivalência de Componentes
@quitomoreno @quitomoreno olá! descubra primeiro o encapsulamento dele. Ele tem algo gravado no corpo? https://en.wikipedia.org/wiki/Small-outline_transistor -
 resolvido Gigabyte- H61m-d2-b3- nao reconhece memoria
SystSoftPcCelTv respondeu o tópico de valmorsantos em Casos Resolvidos - Motherboards PCs
@valmorsantos ótimo! Mude seu tópico para resolvido, basta editar sua primeira postagem de "em analise' para "resolvido'. tá joia! -
 dúvida Integrados SO-8 com thermal pad. Como dessoldar?
SystSoftPcCelTv respondeu o tópico de zazulak em Eletrônica em Geral
@zazulak olá! quando tem uma peça plastica muito próxima do local onde o calor vai ser aplicado - pre aquecer a placa é uma opção mais trabalhosa, porem realmente reduz o tempo do soprador de ar quente sobre o integrado . E como os colegas comentaram usar fida adesiva de alumínio e kapton juntas protegem bem a peça. Ainda podemos inclinar o jato de ar de forma que ele não se direcione para as peças fracas. E em algumas situações protejo com chapinhas de alumínio para servir de Barreira e como a solda ferve usar o soprador com baixa vazão também ajuda a não deslocar outros componentes pequenos - ai mais uma vez o preaquecimento é importante já o ar estará com pouca vazão ainda mais para componentes bga e com as soldas de hoje de prata, por ser mais dura requer mais calor do que antigamente. tá joia!
SOBRE O ELETRÔNICABR
Técnico sem o EletrônicaBR não é um técnico completo! Leia Mais...